Welcome to the definitive resource for understanding and selecting the ideal heavy-duty engine crankshaft for your application. The crankshaft is the backbone of any internal combustion engine, responsible for converting the linear motion of the pistons into the rotational force that powers your vehicle or machinery. In high-stress, high-performance, or heavy-duty environments, a standard crankshaft is simply not enough. The immense forces generated by increased horsepower, torque, and RPMs demand a component built with superior materials, precision engineering, and robust design. Choosing the wrong crankshaft can lead to catastrophic engine failure, resulting in costly repairs and significant downtime.
This comprehensive heavy duty engine crankshaft selection guide is designed to empower everyone, from professional race teams and commercial fleet managers to dedicated enthusiasts building their dream engine. As a leading manufacturer and supplier of high-performance engine components, we believe that an informed customer is a successful customer. We will delve into the critical aspects of crankshaft design, from material science and manufacturing methods to the specific technical specifications that define performance. Our goal is to demystify the selection process, providing you with the knowledge needed to invest confidently in a crankshaft that delivers reliability, durability, and the power you demand.
Section 1: Understanding Crankshaft Fundamentals: Materials and Manufacturing
The journey to selecting the perfect heavy-duty crankshaft begins with a foundational understanding of what sets it apart: the materials it's made from and the process used to shape it. These two factors are the primary determinants of a crankshaft's strength, durability, and, ultimately, its suitability for your specific engine build.
Crankshaft Materials: The Core of Strength
The material composition of a crankshaft dictates its ability to withstand torsional stress, bending forces, and fatigue over millions of cycles. There are three primary materials used in crankshaft construction:
- Cast Iron/Nodular Iron: This is the standard material for most OEM passenger vehicle crankshafts. It is relatively inexpensive and easy to manufacture through casting. While suitable for stock engines and light-duty applications, cast crankshafts lack the tensile strength and ductility required for high-performance or heavy-duty use. They are more brittle and prone to cracking under the stress of high horsepower or sudden shock loads.
- Forged Steel: This is the most popular choice for high-performance and heavy-duty applications. The most common alloy is 4340 forged steel, a high-tensile strength nickel-chromium-molybdenum alloy. The forging process involves heating a steel billet and using immense pressure to press it into the basic shape of a crankshaft. This process aligns the grain structure of the steel, resulting in a component that is significantly stronger, more ductile, and more resistant to fatigue and impact than a cast part. Forged crankshafts offer an excellent balance of strength and cost for the vast majority of performance builds.
- Billet Steel: Representing the pinnacle of crankshaft strength, billet crankshafts are machined from a solid, cylindrical bar (a "billet") of extremely high-quality steel, often an even more robust alloy like 4340 or 300M. There is no forging involved; the entire crankshaft is carved out using sophisticated CNC (Computer Numerical Control) machines. This process allows for complete design freedom and results in a uniform grain structure with no internal stresses from the forging process. Billet crankshafts are the strongest available and are typically reserved for extreme, top-tier applications like professional motorsports or engines producing well over 1,500 horsepower, where budget is secondary to absolute strength and reliability.
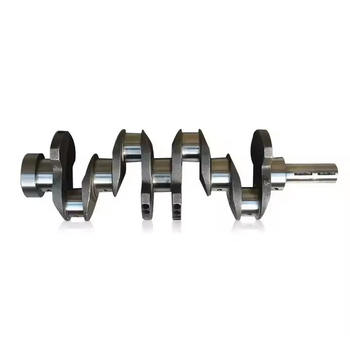
Manufacturing Processes: Shaping for Power
The method used to form the crankshaft is just as critical as the material itself.
- Casting: Molten iron is poured into a sand mold. This is a fast and cost-effective process but can introduce porosity and inconsistencies, creating weak points.
- Forging: As described above, this process refines the steel's grain structure, eliminating porosity and aligning the material's internal fibers with the shape of the crankshaft. This is like comparing a piece of wood carved with the grain versus against it; the one with the aligned grain is far stronger.
- Billet Machining: This is a subtractive process. It offers the highest level of precision and material integrity but is also the most time-consuming and expensive due to the amount of machining required and the material wasted.
For any serious performance or heavy-duty application, the choice is almost always between forged and billet steel. A 4340 forged steel crankshaft is the workhorse of the performance world, while a billet crankshaft is the ultimate solution for when failure is not an option.
Section 2: Decoding Crankshaft Specifications and Design Features
Beyond material and manufacturing, the specific design and dimensions of a crankshaft play a vital role in its performance and how it interacts with the rest of your engine's rotating assembly. Understanding these specifications is crucial for making an informed decision.
Key Geometrical Specifications
- Stroke Length: The stroke is the distance the piston travels from the top of its path (Top Dead Center) to the bottom (Bottom Dead Center). It is determined by the distance from the crankshaft's centerline to the centerline of the rod journals. A longer stroke increases engine displacement, which generally boosts torque, but it can also increase piston speed and side-loading on the cylinder walls, potentially limiting the engine's maximum safe RPM. A shorter stroke is often preferred for high-RPM applications.
- Main and Rod Journal Diameter: The main journals are the surfaces that rotate within the main bearings in the engine block, while the rod journals are where the connecting rods attach. Larger journal diameters create more surface area, which can increase strength and bearing load capacity. However, larger journals also increase rotational mass and surface speed, leading to more friction and heat. Modern engine design often favors smaller, more efficient journal sizes combined with superior materials to maintain strength.
- Post-Machining Treatments: What happens after the crankshaft is shaped is critical for its final durability. Several key treatments enhance its performance:
- Nitriding: A heat-treating process that diffuses nitrogen into the surface of the steel, creating a case-hardened layer. This dramatically increases surface hardness, wear resistance, and fatigue strength, especially on the critical journal surfaces.
- Shot Peening: A process where the surface is bombarded with small, spherical media ("shot"). Each impact acts like a tiny peening hammer, creating a small indentation or dimple. This induces a compressed layer of stress on the surface, which helps resist the formation of fatigue cracks.
- Micro-Polishing: The journal surfaces are polished to an extremely smooth finish. This reduces friction between the crank and the bearings, lowering operating temperatures and improving bearing life.
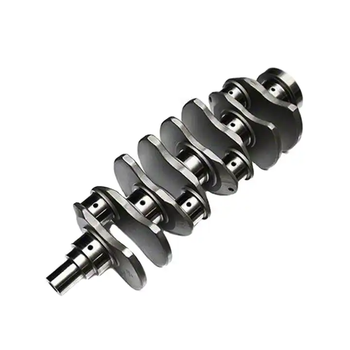
Advanced Design Features
- Counterweight Design: Counterweights are essential for balancing the rotational and reciprocating mass of the pistons and connecting rods. In heavy-duty crankshafts, their design is optimized. "Knife-edged" counterweights are profiled to cut through the oil mist in the crankcase with less resistance, reducing parasitic power loss. "Pendulum undercut" counterweights remove mass from non-critical areas to lighten the crankshaft without sacrificing its balancing effectiveness.
- Lightening Holes: Holes are often drilled in the rod journals to reduce rotational mass. This allows the engine to rev more quickly and reduces the overall inertia of the rotating assembly. The placement and size of these holes are carefully engineered to ensure they do not compromise the journal's structural integrity.
- Oil Passage Design: The design of the internal oil passages is critical for ensuring adequate lubrication reaches the rod bearings, especially at high RPMs. Features like cross-drilling, chamfered oil holes, and straight-shot oiling systems are designed to improve oil flow and prevent bearing starvation.
Section 3: Matching the Crankshaft to Your Engine's Application
With a solid understanding of materials and design, the next step is to match a crankshaft to your specific needs. The ideal crankshaft for a diesel truck used for heavy towing is vastly different from one designed for a drag racing car. This section of our heavy duty engine crankshaft selection guide will help you navigate these choices.
Application-Specific Considerations
- Heavy-Duty Diesel & Towing: These engines operate at lower RPMs but produce immense torque. The primary need is for torsional rigidity and fatigue resistance. A 4340 forged steel crankshaft is an excellent choice here. Stroke is typically kept long to maximize torque, and robust, full-profile counterweights are essential to smoothly handle the heavy pistons and rods. Durability and long service life are prioritized over reducing weight.
- Street Performance / Muscle Car: This is a balanced application. The engine needs to be responsive and powerful but also durable and drivable on the street. A 4340 forged steel crank is again the go-to option. The choice of stroke depends on the desired engine character—a "stroker" crank can add significant torque and horsepower, making it a popular upgrade. A good balance of strength, weight, and cost is key.
- Forced Induction (Turbocharged/Supercharged): Forced induction dramatically increases cylinder pressure, placing immense bending loads on the crankshaft. This is where material strength is paramount. While a high-quality forged crank can handle moderate boost levels, high-boost applications (e.g., over 20 psi) often necessitate a move to a billet steel crankshaft. The superior material integrity of billet steel provides the ultimate insurance against failure under extreme pressure.
- Circle Track / Road Racing: These applications involve sustained high-RPM operation. A lightweight crankshaft is highly desirable to allow the engine to accelerate and decelerate quickly. This often means using a billet crank with knife-edged counterweights, significant lightening, and a shorter stroke. Durability over long races is critical, so premium materials and surface treatments like nitriding are non-negotiable.
- Drag Racing: This is an environment of extreme, instantaneous shock loads. Engines can produce thousands of horsepower. Billet crankshafts are almost universally required at the professional level. The design is focused on maximum strength to handle the violent acceleration, with weight reduction being a secondary but still important consideration.
Decision Checklist:
Ask yourself these questions to narrow down your choice:
- What is my maximum expected horsepower and torque? (Be realistic! Over 800 HP points toward high-end forged or billet. Over 1500 HP almost always requires billet.)
- What is my target RPM range? (High RPMs above 7,500 may benefit from a lighter, shorter-stroke crank.)
- Will the engine be naturally aspirated or forced induction? (Forced induction demands a stronger material.)
- What is the primary use? (Daily driver, weekend racer, heavy towing, dedicated competition?)
- What is my budget? (A forged crank offers the best performance-per-dollar, while a billet crank is a premium investment in ultimate reliability.)
Section 4: Our Unwavering Commitment to Manufacturing and Quality
A crankshaft is only as good as the precision and care put into its manufacturing. As a premier supplier, we stake our reputation on every component that leaves our facility. Our commitment to quality is not just a statement; it is a rigorous, multi-stage process that ensures every crankshaft we produce meets and exceeds the highest industry standards.
Our production process begins with sourcing only the finest certified materials, whether it's vacuum-degassed 4340 forged steel or premium billet bar stock. We maintain full material traceability from the mill to the finished product. Our manufacturing facility is equipped with state-of-the-art, multi-axis CNC machining centers that allow us to hold incredibly tight tolerances, often measured in the ten-thousandths of an inch (0.0001").
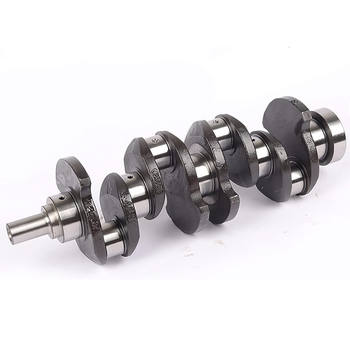
A Culture of Quality Control
Quality is embedded in every step of our workflow. We do not rely solely on a final inspection; we implement checks throughout the entire manufacturing process. Our quality assurance protocol includes:
- Coordinate Measuring Machine (CMM) Inspection: Every critical dimension, from journal diameter and concentricity to stroke and index, is verified on a computer-controlled CMM to ensure perfect geometry.
- Magnaflux Testing (Magnetic Particle Inspection): After machining, every single crankshaft is subjected to magnaflux testing. This non-destructive test reveals any potential surface imperfections or cracks that are invisible to the naked eye, ensuring the part is structurally flawless.
- Hardness and Surface Finish Testing: We verify the depth and consistency of our nitriding process and use profilometers to ensure the journal surface finishes meet our strict specifications for low friction and optimal bearing life.
- Precision Balancing: Every crankshaft is dynamically balanced to exacting standards. A perfectly balanced crankshaft reduces harmful vibrations, which frees up horsepower and dramatically extends the life of the engine bearings and other components.
Our facility is proud to operate under quality management principles aligned with standards like ISO 9001, reflecting our dedication to process control, continuous improvement, and customer satisfaction. When you choose one of our crankshafts, you are choosing a product born from a culture of engineering excellence.
Section 5: Partnering With Us: Flexible Purchasing and Expert Support
We understand that our customers have diverse needs. Whether you are a large-scale engine builder requiring a bulk shipment of components or an individual enthusiast meticulously planning a personal project, we are structured to serve you effectively. We pride ourselves on being more than just a parts supplier; we aim to be your trusted partner in performance.
Flexible Purchasing for All Customers
- Wholesale & B2B Accounts: We offer dedicated programs for commercial clients, including engine builders, performance shops, and racing teams. These accounts feature preferential pricing, volume discounts, and dedicated account management to streamline your procurement process.
- Individual & Retail Sales Welcome: We believe everyone should have access to professional-grade components. We welcome individual purchases and are happy to provide the same level of expert advice and quality products to enthusiasts and small shops.
- Flexible Minimum Order Quantities (MOQs): For our business clients, we offer flexible MOQs to help you manage inventory and cash flow effectively. We can accommodate everything from small-batch orders to full production runs.
Customization and After-Sales Service
Sometimes, an off-the-shelf part isn't quite right for a unique or highly specialized build. Our engineering and manufacturing capabilities allow us to offer a range of customization services:
- Custom Stroke and Journal Sizes: We can manufacture crankshafts to your exact specifications for unique engine displacements or to accommodate custom connecting rods or engine blocks.
- Custom Material Specifications: For extreme applications, we can work with specialized steel alloys to meet specific strength or weight targets.
- Prototyping Services: We can partner with you to develop and manufacture prototype crankshafts for new engine development programs.
Our relationship with you doesn't end after the sale. We provide comprehensive after-sales support, including detailed technical assistance, installation guidance, and robust warranty coverage. Our team of experienced engineers and engine specialists is available to answer your questions and ensure you get the maximum performance and reliability from your investment. We are confident that this complete support system, combined with our technical expertise, makes us the best source for your next project.
For more detailed information, please visit our official website:heavy duty crankshaft
About the author: Dr. Alistair Finch is our Chief Metallurgist and Engine Component Engineer, with over 25 years of experience in the high-performance automotive industry. Holding a Ph.D. in Material Science, his work focuses on the fatigue life and failure analysis of forged and billet steel components under extreme stress. Dr. Finch leads our quality assurance and R&D teams, ensuring every crankshaft we produce is a benchmark for strength, precision, and reliability in the field.